INTRODUCTION
Plastics, which are used in the food industry at the points where there is a possibility of direct or indirect contact with food, have begun to be defined as a potential food safety risk today. Plastics threaten sustainable environmental and public health targets with their uncontrolled waste and residues during their production, use and post-use stages [Chang et al., 2020; Frias & Nash, 2019; Pérez-Guevara et al., 2022].
Microplastic particles (MP) are small particles of plastic waste from 1 μm to 5 mm in size [Chang et al., 2020; Fournier et al., 2021]. Primary MP are industrially used microbeads in different sizes and are released into the environment during production and transportation stages. Microplastics released into the air, soil and seas due to the decomposition of plastic materials and garbage under environmental conditions are defined as secondary microplastics. They are the primary source of microplastics. Microplastics emitted by the friction of tools and equipment used in food production and microplastics emitted from clothes containing polymers are other secondary sources of food contamination [Andrady, 2017; Da Costa Filho et al., 2021; Song et al., 2021].
Many harmful effects of microplastics on living organisms have been revealed. Research on many health concerns is still ongoing. In addition to being a risk that causes trauma to organs and tissues, they can also contain chemical and biological hazards [Allan et al., 2021; Toussaint et al., 2019]. MP from waste may harbour environmental pollutants such as heavy metals, antibiotics, hormones, pesticides, drugs, detergents, disinfectants, and microorganisms. They can also act as a carrier for toxic chemicals known as plastic additives [Chen et al., 2020; Ragusa et al., 2021; Yong et al., 2020]. MP may pose four risks: gastrointestinal toxicity, liver toxicity, neurotoxicity, and reproductive toxicity [Chang et al., 2020]. MP are also the medium for biofilm formation and allow pathogenic microorganisms, a significant potential threat, to enter the body [Qiang et al., 2021]. MP have been demonstrated to pass through the placental barrier, which is known to be permeable to a wide range of toxic substances [Ragusa et al., 2021].
MP are frequently taken orally as well as inhaled. Food and water are considered essential carriers at this point [Yong et al., 2020 have been reported in many food products, including marine invertebrates, crustaceans, fish [Street & Bernasconi, 2021; Waring et al., 2018], table salt [Gündoğdu, 2018; Kosuth et al., 2018], sugar [Liebezeit & Liebezeit, 2013], beer [Kosuth et al., 2018], water [Kosuth et al., 2018; Mason et al., 2018; PérezGuevara et al., 2022; Schymanski et al., 2018; Wiesheu et al., 2016], soft drinks [Shruti et al., 2020], honey [Liebezeit & Liebezeit, 2013, 2015], and broilers [Huang et al., 2020; Kedzierski et al., 2020].
Our research has been focused on the ayran processing steps in a dairy factory with an average daily production of 50,000 L. This traditional and industrially produced Turkish product is encouraged for consumption by people of all ages [TNG, 2015]. Ayran is defined as “a fermented milk product produced by adding drinkable water and salt when necessary, or by adding drinkable water to milk, yogurt bacteria, and if necessary, adding salt after fermentation, by its technique” [TSI, 2013]. The assessment of microplastic contamination in the industrial production process is very important. It was discovered that there is a need for food production process-oriented research when previous studies were examined. In addition to the lack of research on ayran, evaluation of the production process has never been emphasized in a food-related study.
This study aims to investigate the presence of microplastic particles in the industrial production of ayran and to identify the potential sources of contamination at various stages of production.
MATERIALS AND METHODS
Sample collection
The samples for the study were collected from the ayran production line at a Turkish dairy plant in Istanbul with an average daily production of 50,000 L. The process steps were monitored and recorded on-site. Control points were noted in the workflow chart according to the food safety management system applied in the enterprise. The study was repeated on five different days, and parallel sampling was done every sampling day. A total of 180 samples were collected throughout the production process from all process steps, inputs, outputs, and materials that may have been contaminated with microplastic. The scheme of process steps and sampling locations are shown in Figure 1.
Prior to the acceptance of raw milk into the facility, the walls of the stainless-steel raw milk tank (Z) were rinsed with microplastic-free ultrapure water, and a 1,000 mL sample was taken. The samples (1,000 mL or 1,000 g) were collected during raw milk acceptance (RM), filtration (F), clarification (C), water addition (WA), homogenization (H), pasteurization (P), holder (Q), starter culture addition (SCA), salty water addition (SWA), and filtration before filling (FB). In addition, samples of water (tap water, W), separated cream (CR), ready-to-use starter culture (SC), salt (S), salty water (SW), filling ayran cups (AC), and the ready-to-drink ayran (A) were collected. A 1,000 mL sample of ready-to-use starter culture and a 500 g sample of the salt were taken. Microplastic-free ultrapure water was added to the salt to make it up to 10 L and dissolved. A collected sample of 1,000 mL of the solution was filtered. The empty ayran cups were refilled with 1,000 mL of microplastic-free ultrapure water and sealed before being transported to the laboratory with all samples.
Digestion of organic matter of the samples
The method for digestion of organic matter of the samples proposed by Da Costa Filho et al. [2021] was followed. Each milk, separated cream, ready-to-use starter culture and ready-to-drink final product (ayran) sample was transferred to an Erlenmeyer flask cleaned with microplastic-free ultrapure water before analysis. Ayran, cream and ready-to-use starter culture were challenging to filter through due to their density. Therefore, these samples were homogenised by vigorously shaking with twice the volume of ultrapure water in an Erlenmeyer flask. This step was not necessary for the milk samples. Next, 25 mL of the samples were mixed with 20 mL of microplastic-free ultrapure water. An aliquot of 2 mL of multi-enzymatic detergent containing protease, amylase, lipase, and cellulase (Deconex® Prozyme Active, Boer Chemie, Zuchwil, Switzerland) was added. The samples were stirred for 2 min at 40°C. Then, 10 mL of ethylenediaminetetraacetic acid (EDTA, Thermo Fisher Scientific, Waltham, MA, USA) was added and stirred at 40°C for 3 min. Finally, 2 mL of tetramethylammonium hydrate (Merck, Darmstadt, Germany) was mixed into the mixture. Samples were incubated at 80°C for 1 min and filtered immediately. The direct filtering stage was started for water, salt, and salty water samples.
Sample filtration
Before and after each sample filtration, all filtration equipment was thoroughly cleaned with microplastic-free ultrapure water. Filtration was carried out at a pressure of approximately 0.5–0.6 bar using glass microfiber filters with a pore size of 1 μm (Whatman grade GF/B glass microfiber filters, diameter 47 mm, Cytiva Marlborough, MA, USA) and a vacuum pump [Kosuth et al., 2018; Liebezeit & Liebezeit, 2015; Schymanski et al., 2018]. At least two replicates of the same samples (each of 100 mL) were processed. Using metal tweezers, the filters were transferred carefully into glass Petri dishes. They were then stored for analysis after being air-dried at room temperature.
Optical microscopy analysis
After filtrations, the glass microfiber filters were viewed under the Olympus CX31 optical microscope (Olympus, Tokyo, Japan) with Canon A640 camera (Canon, Tokyo, Japan) using 4× magnification. The number of microplastic particles per volume or weight of sample (MP number/100 mL or MP number/100 g, respectively) was adopted as the unit of quantification. Using Kameram software 1.3.0.8 (Mikrosistem, Istanbul, Turkey), microparticles were captured on film. Using IC Measure software 2.0.0.286 (The Imaging Source, Bremen, Germany), the particles’ longest side was measured and classified by colour, shape, and size.
Scanning electron microscopy and Fourier-transform infrared spectroscopy analyses
The morphology of randomly selected microplastics was analysed by scanning electron microscopy (SEM). The images were taken using high-resolution SEM microscope (JSM-7001F, Jeol, Tokyo, Japan) in high vacuum pressure mode operating at 10.00 kV acceleration voltage, in secondary electron and backscattering modes and different magnifications. The filter parts containing the microplastic particles were marked with an architectural drawing pen under the optical microscope, cut with scissors, and carefully transferred with metal tweezers onto double-sided carbon adhesive tape mounted on aluminium SEM pin stubs.
The chemical composition of microplastics was identified using Fourier-transform infrared spectroscopy (FTIR) analysis. Agilent Cary 630 spectrometer (Agilent, Santa Clara, CA, USA) within the 400–4000 cm−1 range, 8 scans, and 4 cm−1 resolutions was used. The results were evaluated using Agilent Polymer Handheld ATR, Agilent Elastomer Oring and Seal Handheld ATR and Agilent ATR General Libraries.
Procedures adopted to ensure the accuracy of the experiments
Several precautions proposed by Wang et al. [2017] were taken in the experiments, from field sampling to laboratory analysis, to ensure the accuracy of results. Cotton lab coats and nitrile gloves were worn to prevent contamination of the samples by airborne polymer particles and fibres. All consumables used were made from glass and stainless steel to avoid plastic contamination. The surfaces were cleaned with microplastic-free ultrapure water and acetone, and the contamination was tried to be reduced to a negligible level or zero. Before filtration, each filter paper package was opened and eventually microplastic contamination of filters was evaluated under the optical microscope. No microplastic contamination was detected in any of them.
Experimental blanks were conducted in all selected sampling locations. At each location, 1,000 mL of MP-free ultrapure water was blank sample [Chae et al., 2015; Dubaish & Liebezeit, 2013; Nuelle et al., 2014]. Each analysis was carried out in five replications. Analyses for blank samples were conducted according to the same procedure as that for water samples. Finally, under the microscope, an average of 0.05±0.04 MP number/L were detected in blank samples.
Samples were analysed in a laminar cabinet, therefore potential MP in the air were examined with Petri dishes with filters placed next to the samples in a laminar flow cabinet and left open for 1 h, which allowed obtaining data about the level of contamination. On average, 0.13±0.06 MP number/h were found under the microscope.
Multi-enzymatic detergent, EDTA and tetramethylammonium hydrate were controlled for microplastics. Before use, empty sample bottles were rinsed with microplastic-free ultrapure water (1,000 mL), and this water was analysed to investigate the glass bottles’ microplastic particle presence. The results of these tests confirmed the absence of contamination. Microplastic-free ultrapure water was included in the analysis protocol as a blank control.
Positive control analysis
Polypropylene (PP), polystyrene (PS), polyethylene (PE), polyvinyl chloride (PVC), linear low-density polyethylene (LLDPE), and thermoplastic elastomers (TPE) were used as positive controls. The sources of these materials were described in Table S1. All positive samples’ chemical composition was identified using FTIR. Plastic materials were ground first with an oscillating mill (Retsch MM 400, Haan, Germany) and then with ultraturrax (IKA T 25, Staufen im Breisgau, Germany). Each crushed plastic material (1 mg) was mixed with 1,000 mL of microplastic-free ultrapure water in a microplastic-free glass bottle. After standing overnight, the mixture was subjected to filtration. At least ten replicates of the same samples were processed. Before positive control sample filtration, all safety precautions were taken, as described in the section “Procedures adopted to ensure the accuracy of the experiments”. Filtration and optical microscopy analysis were done as described above. Each filter was rinsed with 1,000 mL of microplastic-free ultrapure water in a microplastic-free glass bottle and left overnight.
Calculation of microplastic particle ingestion by humans
The risk assessment was based on the total amount of microplastic particles ingested orally. It has been presumed that drinking ayran provides the entire amount of dairy products recommended for daily diet consumption. This evaluation did not took into account any toxicokinetic components. According to the recommendations of the Turkey Nutrition Guide [TNG, 2015], it was assumed that the daily amount of ayran for adult is three servings (1 serving = 240 mL). Children, adolescents, pregnant-breastfeeding women, and postmenopausal women should consume two to four servings, i.e., 720 mL and 480–960 mL of ayran, respectively, per day. Daily intake of MPs with ayran was calculated using Equation (1):
where: EDI, estimated daily intake of MPs with ayran (MP number/ day); W, recommended amount of ayran (mL/day); C, microplastic content (MP number/100 mL).RESULTS AND DISCUSSION
Our study investigated the risk of microplastic contamination in the industrial production processes of ayran, a traditional Turkish beverage. Ayran production processes had been evaluated step by step, and the sources of the hazard had been determined. The microplastic load, type, size, colour, and shape were assessed at each production stage. According to our literature search, although there are studies in different scopes and scales on microplastic contamination of various foods such as honey, salt, sugar, soft drinks, beer, alcohol, meat, broilers, especially seafood and water [Cox et al., 2019; Kedzierski et al., 2020; Toussaint et al., 2019], this is the first study to investigate microplastics’ existence in a food production line.
Before and during the study, experimental blank tests were conducted at all selected sampling sites, laboratory areas, ultrapure water, chemicals, instruments and equipment. Experimental blank tests and ultrapure water filtration results to ensure safe analysis conditions revealed that background contamination was minimal and negligible. The filtration and optical microscopy analysis results of the positive control samples’ colour, shape, and size distribution are given in Table S2. As a result of the study conducted to evaluate the method performance, the recovery rates of PP, PS, PE, PVC, LLDPE, and TPE were 98±2%, 96±4%, 95±4%, 87±7%, 89±6%, and 91±9%, respectively. These results indicated the method’s reliability.
As understandable in the results of this study, microplastic contamination is probable in the ayran production process steps. Microplastic particles were detected in all examined samples except the ready-to-use starter culture. However, the quantities of microplastic particles varied significantly between processing steps (Table 1). The samples with the highest microplastic count were found to be salty water (43 MP number/100 mL), salt (33 MP number/ 100 g), and milk samples from homogenization and pasteurization steps (26 MP number/100 mL). There were total of 313 microplastic particles on the filters of 17 process steps/sampling locations. Microplastics were abundant between 3 and 43 MP number per 100 mL or per 100 g. An average of 19 MP number/100 mL of raw milk on five different production days was determined. This contamination of the raw material was a determinant of the quality of the last product (ayran).
Table 1
Abundance of microplastic particles (MP) and their size in samples collected during ayran production at different process steps/sampling locations.
[i] Z, bulk tank; RM, raw milk acceptance; F, filtration; C, clarification; W, water; WA, water addition; CR, cream; H, homogenization; P, pasteurization; Q, holder; SC, ready-to-use starter culture; SCA, starter culture addition; S, salt; SW, salty water; SWA, salty water addition; FB, filtration before filling; AC, filling ayran cups; A, ready-to-drink ayran; SD, standard deviation.
Examining the production and logistics of milk and dairy products revealed several potential microplastic contamination risk points. Plastic pipes, valves and fittings used to pour milk into tankers and transport it to the dairy plants can be a significant source of contamination for microplastic. Tankers carrying milk from milk collection points to dairy production facilities can be considered a risk factor. The water, detergents, disinfectants used for clean in place (CIP), hoses for water transfer, and rubber pipes may pose a risk to the microplastic load [Britz & Robinson, 2008; Walstra et al., 2005]. The other contamination locations are refrigerated storage tanks at farms, stainless steel containers, buckets, and rubber rings of automatic milking units. In addition to cloths, brushes, gloves, and other plastic cleaning equipment, detergents, disinfectants, and water may also be a source of contamination [Caramia & Guerriero, 2010; Lopes & Stamford, 1997]. Due to the expiration of their useful life, poor quality of the polymer used, or unanticipated external factors, a variety of polymers used in the equipment of the food industry may be a source of microplastic contamination in foods [Nady, 2016; Pouliot, 2008; Tan & Rodrigue, 2019]. All seals and filtration units that are not maintained periodically are another important source of contamination. The enlargement of the filter pores by the microplastics, organic materials, mineral substances, and colloids trapped in the filters during the pressurised liquid The surface morphology of two representative microflow can increase the risk of contamination of the milk with plastics observed using SEM is given in Figure 2. SEM is microplastics [Kumar et al., 2013; Tomasula & Bonnaillie, 2015].
Figure 2
Scanning electron microscopy (SEM) image of microplastic particles: A, ethylene propylene (raw milk); B, ethylene propylene (water); C, polytetrafluoroethylene (water); D, polytetrafluoroethylene (ready-to-drink ayran).
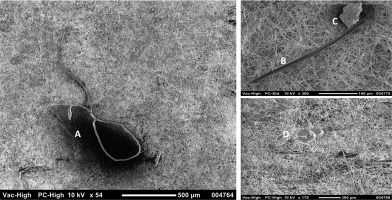
The surface morphology of two representative micro plastics observed using SEM is given in Figure 2. SEM is a microscopic technique that can provide information about the morphological surface structure of MP, producing high-resolution images of the surface state. It can also provide data on the chemical composition of samples, as it can be equipped with energy dispersive X-ray spectroscopy (EDS) detectors. In our study, an overview of the structures of the particles present was provided by SEM imaging of randomly selected filter surfaces after optical microscopy analysis. However, SEM imaging did not provide enough discriminatory evidence to confirm that the analysed microparticle was an MP or organic residue. Mineral-based particles can be identified through EDS analysis [Mariano et al., 2021]. However, in the trial studies, it was determined that the fibers, organic residues and MP showed similar spectra for C, O and N elements. Therefore, as some researchers have noted, SEM-EDS can be used as a tool to support FTIR, but it has not been shown to be sufficient alone for the identification of MP [Da Costa Filho et al., 2021; Mariano et al., 2021].
Selected optical microscopy images of microplastic particles detected at various stages of ayran production are shown in Figure 3. The particles varied in size and shape. The distribution of microplastic particle size in samples was summarised in Table 2. Microplastic particles with a size range of 1–150 μm (37.38%) prevailed. In addition, 36.42% of the microplastic particles had between 151 and 1,000 μm in size, while size of 26.20% of the particles ranged from 1,001 to 5,000 μm. Microplastic particle size is an essential parameter for translocation in living organisms. This parameter determines the microplastic absorption efficiency through the gastrointestinal, alveolar, and dermal epithelium. After oral ingestion, microplastics and nanoplastics can be dispersed into the blood and lymphatic system, and subsequently the liver, via absorption from the gastrointestinal tract. The gastrointestinal epithelium is permeable to particles of 150 μm, >90% of those larger than 150 μm are excreted in the faeces [Dick Vethaak & Leslie, 2016; Kannan & Vimalkumar, 2021]. It has been reported that intestinal absorption of MP smaller than 1.5 μm is possible, and MP smaller than 2.5 μm can enter the systemic circulation via endocytosis and phagocytosis [Dris et al., 2016; EFSA, 2016; Hwang et al., 2020; Kannan & Vimalkumar, 2021; Millburn et al., 1967; Yang et al., 2009]. However, particles of 0.1 μm and smaller can cross the blood-brain barrier and placenta [Prietl et al., 2014]. In our study, microparticles smaller than 10 μm were detected only in the raw milk acceptance sample and they accounted for 5.26% of all particles. The filter pore diameter used in filtration does not allow the detection of smaller particles. When discussing the dangers posed by microplastics in food, focus is more on their physical effects and the effects of the endocrine-disrupting ingredients they contain, such as bisphenol A, phthalates, and certain brominated flame retardants. Due to these factors, microplastics can cause serious health problems [Dick Vethaak & Leslie, 2016]. Studies demonstrate that microplastic causes intestinal microbiota changes in mice and gastric adenocarcinoma in humans [Chang et al., 2020]. It has been shown that the consumption of microplastic reduces key gene expressions related to lipogenesis and triglyceride synthesis in the liver, which can lead to mouse hepatic lipid disorder [Lu et al., 2018].
Figure 3
Optical microscopy images of microplastic particles in samples collected during ayran production. A, 3679.22 μm, ethylene propylene (raw milk); B, 468.42 μm, ethylene propylene (water); C, 98.02 μm, polytetrafluoroethylene (water); and D, 215 μm polytetrafluoroethylene (ready-to-drink ayran).
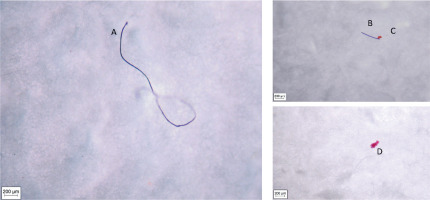
Table 2
Number of microplastic particles (MP) with different size in samples collected during ayran production at different process steps/sampling locations (MP number/100 mL or MP number/100 g).
Process step/sampling location | 1–10 μm | 11–50 μm | 51–150 μm | 151–500 μm | 501–1,000 μm | 1,001–5,000 μm |
---|---|---|---|---|---|---|
Z | – | – | 1 (33.33%)* | 1 (33.33%) | – | 1 (33.33%) |
RM | 1 (5.26%) | 1 (5.26%) | 6 (31.58%) | 2 (10.53%) | 1 (5.26%) | 8 (42.11%) |
F | – | 4 (23.53%) | 5 (29.41%) | 2 (11.76%) | 2 (11.76%) | 4 (23.53%) |
C | – | 2 (12.50%) | 4 (25.00%) | 4 (25.00%) | 2 (12.50%) | 4 (25.00%) |
W | – | 4 (21.05%) | 7 (36.84%) | 6 (31.58%) | 1 (5.26%) | 1 (5.26%) |
WA | – | 1 (7.69%) | 4 (30.77%) | 3 (23.08%) | 2 (15.38%) | 3 (23.08%) |
CR | – | – | 1 (11.11%) | 7 (77.78%) | 1 (11.11%) | – |
H | – | 2 (7.69%) | 9 (34.62%) | 3 (11.54%) | 3 (11.54%) | 9 (34.62%) |
P | – | 1 (3.85%) | 8 (30.77%) | 6 (23.08%) | 4 (15.38%) | 7 (26.92%) |
Q | – | 2 (22.22%) | 2 (22.22%) | 2 (22.22%) | 1 (11.11%) | 2 (22.22%) |
SC | – | – | – | – | – | – |
SCA | – | 1 (8.33%) | 3 (25.00%) | 4 (33.33%) | 3 (25.00%) | 1 (8.33%) |
S | – | 4 (12.12%) | 10 (30.30%) | 11 (33.33%) | 4 (12.12%) | 4 (12.12%) |
SW | – | 3 (6.98%) | 8 (18.60%) | 7 (16.28%) | 1 (2.33%) | 23 (53.49%) |
SWA | – | 3 (18.75%) | 4 (25.00%) | 2 (12.50%) | 2 (12.50%) | 4 (25.00%) |
FB | – | 2 (9.52%) | 4 (19.04%) | 3 (14.29%) | 3 (14.29%) | 9 (42.86%) |
AC | – | 1 (7.69%) | 5 (38.46%) | 4 (30.77%) | 2 (15.38%) | – |
A | – | 2 (11.11%) | 6 (33.33%) | 7 (38.89%) | 3 (16.67% | – |
* Percentage of the number of microplastic particles in the sample is given in brackets Z, bulk tank; RM, raw milk acceptance; F, filtration; C, clarification; W, water; WA, water addition; CR, cream; H, homogenization; P, pasteurization; Q, holder; SC, ready-to-use starter culture; SCA, starter culture addition; S, salt; SW, salty water; SWA, salty water addition; FB, filtration before filling; AC, filling ayran cups; A, ready-to-drink ayran.
Microplastic particles were visualised using optical microscope in black, blue, brown, dark blue, grey, green, orange, pink, purple, red, transparent, and yellow. The visualization showed that 19.81% of the microplastic particles were recorded as blue, 17.89% as red, 15.02% as transparent, and 11.18% as black (Figure 4). The microplastic particles varied also in shape. Fibre form dominated (49.84%), followed by film (23.32%), fragments (14.70%), and spheres (12.4%) (Table 3). According to RodriguezSeijo & Pereira [2017], colours are crucial for visually distinguishing the chemical composition of microplastics. The chemical composition of microplastics can provide clues in predicting the type of polymer from which the food contact or likely to come into contact with tools, equipment, materials, packaging materials. This data is valuable to identify the source of food contamination [Nady, 2016; Pouliot, 2008; Tan & Rodrigue, 2019]. In our study, the FTIR data of microplastics (discussed below) revealed that colour would not be a sufficient clue for chemical characterisation. The colour detected under a microscope may depend on the colour pigments and additives used in producing plastic materials; it cannot be associated with the type of polymer [Oßmann et al., 2018].
Figure 4
Number of microplastic particles with different colour in samples collected during ayran production at different process steps/sampling locations: Z, bulk tank; RM, raw milk acceptance; F, filtration; C, clarification; W, water; WA, water addition; CR, cream; H, homogenization; P, pasteurization; Q, holder; SC, ready-to-use starter culture; SCA, starter culture addition; S, salt; SW, salty water; SWA, salty water addition; FB, filtration before filling; AC, filling ayran cups; A, ready-to-drink ayran.
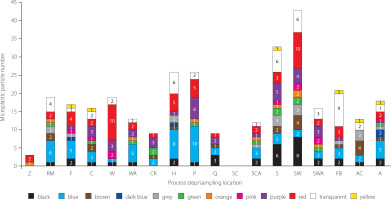
Table 3
Number of microplastic particles (MP) with different shapes and microplastic polymer type in samples collected during ayran production at different process steps/sampling locations (MP number/100 mL or MP number/100 g).
Polymer type | Polymer shape | Z | RM | F | C | W | WA | CR | H | P | Q | SC | SCA | S | SW | SWA | FB | AC | A |
---|---|---|---|---|---|---|---|---|---|---|---|---|---|---|---|---|---|---|---|
EP (39.30%)* | Fibre | 1 | 7 | 6 | 5 | 5 | 8 | 8 | 6 | 16 | 1 | 0 | 2 | 8 | 8 | 4 | 10 | 2 | 5 |
Film | – | 1 | – | 1 | – | – | – | 1 | – | – | – | – | – | 1 | 1 | – | 1 | – | |
Fragment | – | 1 | – | – | – | – | 1 | 6 | 1 | 1 | – | – | 1 | – | – | – | 1 | 2 | |
Sphere | – | – | – | – | – | – | – | – | – | – | – | – | – | – | – | 1 | – | – | |
NP (10.22%) | Fibre | – | 1 | – | – | – | – | – | – | – | – | – | – | – | – | – | – | – | – |
Film | – | 2 | – | – | – | 1 | – | 1 | 1 | 1 | – | 1 | – | – | 1 | 1 | 1 | 3 | |
Fragment | – | – | – | – | 1 | – | – | – | – | 1 | – | – | – | 1 | – | – | 1 | 2 | |
Sphere | – | 1 | 1 | – | – | – | – | – | – | 1 | – | – | 3 | 4 | 1 | 1 | – | – | |
PA (3.19%) | Fibre | – | – | – | – | – | – | – | – | 1 | 1 | – | 1 | 1 | – | – | 2 | – | 1 |
Film | – | – | – | – | 1 | – | – | – | – | – | – | – | 1 | – | – | – | – | – | |
Fragment | – | – | – | – | – | – | – | – | – | – | – | – | – | – | – | – | – | – | |
Sphere | – | – | – | 1 | – | – | – | – | – | – | – | – | – | – | – | – | – | – | |
PAM (11.18%) | Fibre | – | 1 | 1 | 1 | – | – | – | 2 | – | 1 | – | 2 | 3 | 4 | 2 | 1 | 2 | 1 |
Film | – | – | – | – | – | – | – | 2 | – | – | – | 1 | 3 | 4 | 1 | 1 | 2 | – | |
Fragment | – | – | – | – | – | – | – | – | – | – | – | – | – | – | – | – | – | – | |
Sphere | – | – | – | – | – | – | – | – | – | – | – | – | – | – | – | – | – | – | |
PE (2.88%) | Fibre | – | – | – | – | – | – | – | – | – | – | – | – | – | – | – | – | – | – |
Film | – | – | – | – | – | – | – | 1 | – | – | – | – | – | – | – | – | – | – | |
Fragment | – | – | – | – | – | – | – | – | – | – | – | – | – | – | – | – | – | – | |
Sphere | – | 1 | 1 | – | – | – | – | 1 | – | – | – | 1 | 2 | 1 | 1 | – | – | – | |
PP (7.35%) | Fibre | – | – | 2 | 1 | 1 | 1 | – | 3 | 3 | 1 | – | 1 | 2 | 2 | 1 | 1 | 1 | – |
Film | – | – | – | – | – | – | – | – | – | – | – | – | – | 3 | – | – | – | – | |
Fragment | – | – | – | – | – | – | – | – | – | – | – | – | – | – | – | – | – | – | |
Sphere | – | – | – | – | – | – | – | – | – | – | – | – | – | – | – | – | – | – | |
PTFE (25.88%) | Fibre | – | – | – | 5 | – | – | – | – | – | – | – | – | – | – | – | – | – | – |
Film | – | 2 | 3 | 1 | 5 | 1 | – | 1 | 2 | 1 | – | 1 | 4 | 7 | 2 | 1 | 1 | 2 | |
Fragment | 2 | – | 3 | 1 | 5 | 1 | – | 1 | 1 | – | – | 2 | 2 | 4 | 1 | 1 | 1 | 1 | |
Sphere | – | 2 | – | – | 1 | 1 | – | 1 | 1 | – | – | – | 3 | 4 | 1 | 1 | – | 1 |
* Percentage of the number of microplastic particles in the sample is given in brackets; EP, ethylene propylene; NP, neoprene; PA, polyamide; PAM, polyacrylamide; PE, polyethylene; PP, polypropylene; PTFE, polytetrafluoroethylene; Z, bulk tank; RM, raw milk acceptance; F, filtration; C, clarification; W, water; WA, water addition; CR, cream; H, homogenization; P, pasteurization; Q, holder; SC, ready-to-use starter culture; SCA, starter culture addition; S, salt; SW, salty water; SWA, salty water addition; FB, filtration before filling; AC, filling ayran cups; A, ready-to-drink ayran.
The FTIR technique used to identify microplastic particles through microscopic imaging detects the FTIR absorption spectrum, reveals the structural fingerprints, and reflects the optical responses of the surface functional groups. In this method, the spectra formed by the absorbance values of the displayed microplastic particles were compared to the spectra of reference polymers in the polymer library [Fan et al., 2021]. The examples of FTIR spectra of MP of samples and reference polymers are given in Figure 5. Seven types of microplastics were identified by FTIR in the samples: ethylene propylene (EP) (39.30%), polytetrafluoroethylene (PTFE) (25.88%), polyamide (PA) (11.18%), neoprene (NP) (10.22%), polypropylene (PP) (7.35%), polyacrylamide (PAM) (3.19%), and polyethylene (PE) (2.88%). FTIR analysis revealed that black microplastics were neoprene, polyamide, and polyacrylamide; blues were EP and PE; browns were PTFE, PP and PAM; dark blues were NP, EP, and PE; greys were NP, PA, and PAM; greens were EP; oranges were PTFE; pinks were PTFE and PP; pink and red ones were PTFE and PP; purples were EP, PAM, PA, PP, and PTFE; transparent were EP, NP, PAM, and PA; yellows were PAM and PTFE. The EP, which was identified in the samples of our study, is used as an air and water-sealing gasket; neoprene is used as an oil-sealing gasket in dairy facilities. PAM finds use in agricultural lands for erosion control and improving the physical properties of the soil. Very small amounts of PAM in irrigation water were reported to flow over the soil in irrigation troughs, virtually eliminating the separation and transport of soil particles [Sojka et al., 2007]. PTFE, which is very common in the environment, is seen in milk as a sign of environmental contamination. A series of macro-, micro and ultrafiltration processes using polymeric membranes, from the milking process to the packaging of the products, can be considered a source of PTFE [Diaz-Basantes et al., 2020; Kutralam-Muniasamy et al., 2020]. PAs replace metal parts in engine components as tough, corrosion-resistant, lighter, and more cost-effective intake manifolds. They are also used as an alternative insulation material for electrical cables. Reinforcing polyamides with typically 30% glass fibres makes them so resilient that they can be used as a metal substitute. In this form, they can be used as building elements. Additionally, they can also be preferred as packaging materials. In wastewater treatment plants, PE is used to produce tanks, equipment, pumps, valves, diaphragms, bellows, and cylinders. Additionally, moving machine parts, toothed wheel rollers, sliding equipment, and conveyor equipment construction are its other uses in the food industry. PP is used in producing beverage containers and bottles in various shapes and capacities. Also, it is a polymer used to preserve cleaning agents, disinfectants and chemical reagents [Pouzada, 2021].
Figure 5
Fourier-transform infrared spectroscopy (FTIR) spectra of microplastic particles of samples collected during ayran production and reference polymers: (A) ethylene propylene, (B) neoprene, (C) polyacrylamide, (D) polyamide, (E) polyethylene, (F) polypropylene, and (G) polytetrafluoroethylene.
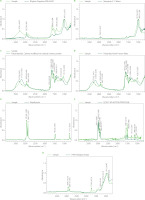
The EDI, which shows the number of microplastics that can be daily swallowed with ayran, was calculated according to the Turkish Nutrition Guide [TNG, 2015]. It was estimated that adults could consume 259±2 MP number/day, and children, adolescents, pregnant-breastfeeding women, and postmenopausal women from 173±14 to 346±7 MP number/day. The risk assessment reveals the total amount of microplastics ingested and the physical distribution of microplastics in the human body. It excludes toxicological hazards associated with the composition of polymers, bacterial film formation on the surface of microplastics, and possible microbiological considerations such as the presence of viruses. It does not indicate ingested microplastic’s faecal excretion rate and the intestinal epithelium translocation rate. In a meta-analysis study based on 402 data points from 26 articles representing more than 3,600 processed food samples, Cox et al. [2019] calculated total annual microplastic ingestion by age and body weight to range between 39,000 and 52,000 particles. When inhalation exposure was included, this number has been estimated to range between 74,000 and 121,000. Additionally, they had estimated that people who consume only bottled water are exposed to 90,000 microplastics, compared to 4,000 microplastics for those who consume the recommended amount of water by drinking tap water. Pérez-Guevara et al. [2022] estimated that Mexico City residents accidentally ingested 42 MP/L through drinking water, with annual exposures of approximately 1.47×104 MP per adult and 6.73×103 MP per child. In another study examining the potential exposure of infants to PP microplastics through the consumption of formulas prepared in infant feeding bottles, the exposure ranged from 14,600 to 4,550,000 (mean 1,580,000) microplastics/day per baby, depending on the sampling geographic location. Scenario studies revealed that sterilization and exposure to high temperature water of PP infant bottles significantly increased the release of microplastics. Considering that adults were estimated to consume 600 microplastics per day through water, food, and air, they have determined that infants were exposed to approximately 2,600 times more microplastics per day than adults [Li et al., 2020].
CONCLUSIONS
Studies have revealed the risk of microplastic contamination in the production line of ayran of a medium-sized production facility. Microplastic particles have been detected at each step of production, in raw materials, auxiliary materials, semi-finished materials, and final product. The microplastic particles in the samples collected at different process steps/sampling locations varied in size, colour, shape, and polymer type. Contamination of ayran cups, water, and salt with microplastics was quite severe. Water and salt in food production should be pre-treated with special pore-sized filters against microplastics. Before the filling process, some precaution measures against contamination of cups and bottles with microplastics, like pre-washing with microplastic-free ultrapure water, should be taken. Further studies are needed to detect microplastic contamination sources before the raw milk acceptance step. It is necessary to investigate the content of microplastics in other dairy products, and additional data need to be collected on raw milk contamination with plastic residues.